Mould Tooling Manufacturer China: Quality and Innovation in Metal Fabrication
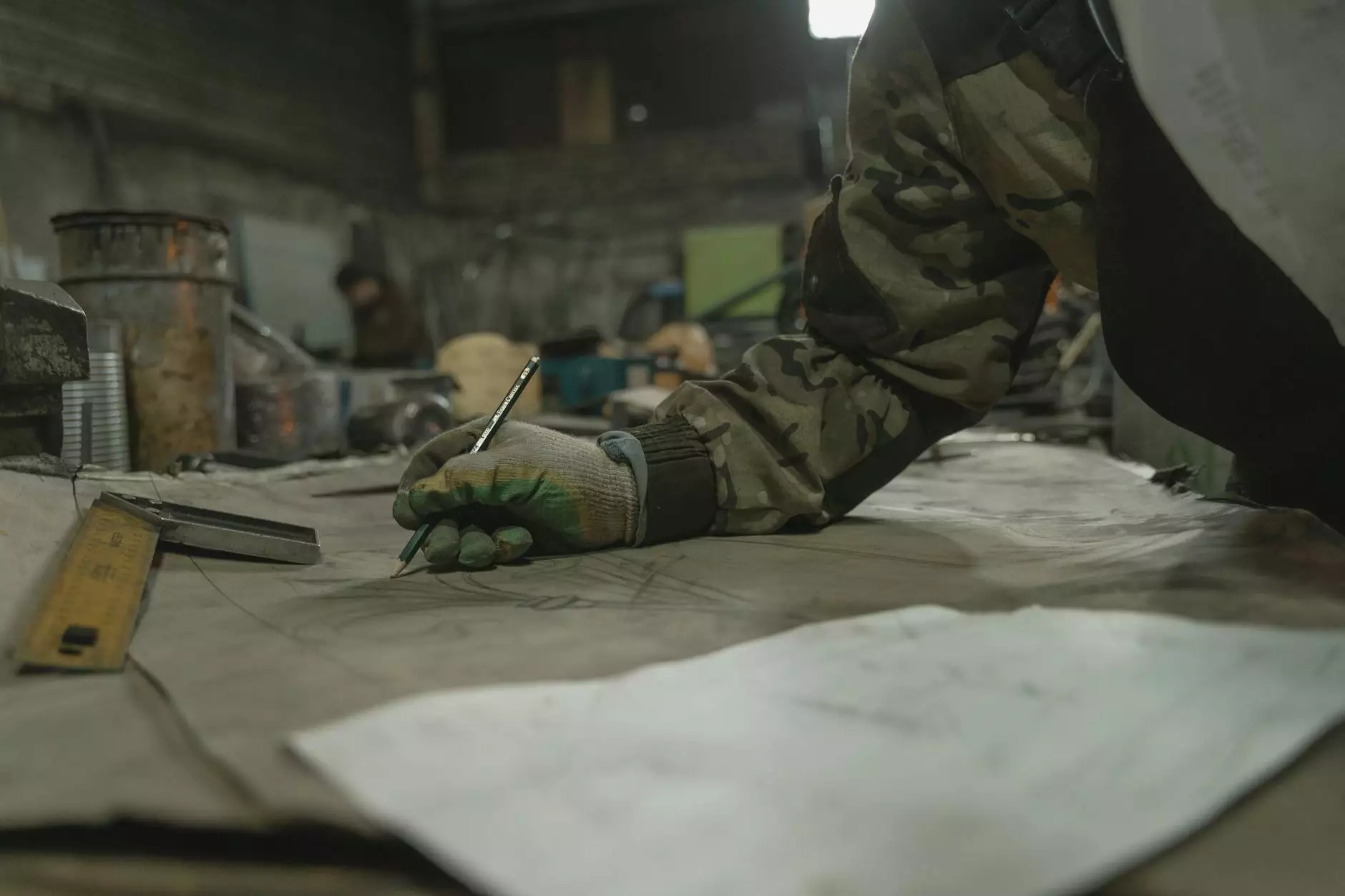
Understanding Mould Tooling
Mould tooling plays a crucial role in the manufacturing industry, especially for companies that specialize in producing high-quality components and products. This intricate process involves designing, creating, and using molds to shape materials into specific configurations. With advancements in technology, the landscape of mould tooling has transformed significantly, making it an essential aspect for businesses looking to achieve precision and efficiency.
In this comprehensive guide, we will explore the various dimensions of being a leading mould tooling manufacturer in China. We will delve into the techniques, advantages, and innovations that make Chinese manufacturers some of the most sought-after solutions providers in the global market.
The Role of Mould Tooling in Manufacturing
The significance of mould tooling cannot be overstated. It serves as the foundation for numerous industries, including automotive, aerospace, consumer goods, and electronics. The process entails various stages:
- Designing: Creating the initial blueprint of the mould based on product requirements.
- Prototyping: Developing prototypes to test the functionality and design accuracy before production.
- Manufacturing: Producing the actual mould using advanced fabrication techniques.
- Testing: Conducting rigorous quality checks to ensure the mould meets required specifications.
- Production: Utilizing the mould in the production process to achieve mass manufacturing.
This complex process involves meticulous planning, precision engineering, and an understanding of material properties to ensure that end products meet high-quality standards.
Why Choose a Mould Tooling Manufacturer in China?
China has firmly established itself as a global leader in manufacturing, particularly in the realm of mould tooling. Here are several compelling reasons why choosing a Chinese manufacturer can benefit your business:
- Cost-Effectiveness: Chinese manufacturers offer competitive pricing due to lower labor costs and optimized manufacturing processes, enabling businesses to reduce production expenses.
- Advanced Technology: Many Chinese mould tooling manufacturers employ state-of-the-art technology and equipment, ensuring high precision and efficiency in production.
- Skilled Workforce: China boasts a large pool of skilled workers who are proficient in modern manufacturing techniques and tailored solutions.
- Scalability: With vast production capabilities, Chinese manufacturers can easily scale operations to meet increased demand.
- Innovative Solutions: Continuous investment in research and development allows manufacturers to implement innovative tooling solutions that can enhance product quality.
Choosing a reliable mould tooling manufacturer in China not only optimizes cost but also improves the overall quality and reliability of your products.
The Manufacturing Process of Mould Tooling
The mould tooling process can vary based on the complexity of the product and the materials used. However, there are standardized steps involved:
Initial Consultation and Design
The process begins with a thorough consultation to understand the client's needs. Engineers and designers collaborate to create a detailed design that encompasses:
- Product specifications
- Material requirements
- Functionality tests
- Cost analysis
Prototype Development
Once the design is finalized, a prototype is produced. This step allows for:
- Testing the design under operational conditions
- Adjusting any discrepancies in the design
- Validating the functionality before mass production
Mould Fabrication
Upon approval of the prototype, the actual mould is fabricated using high-quality materials such as steel or aluminum. This step demands precision machining and attention to detail.
Quality Assurance
Before a mould is shipped, it undergoes stringent quality checks. These checks ensure that the mould meets international standards and the specific requirements set by the client.
Materials Used in Mould Tooling
The choice of materials is critical in the mould tooling process. Various materials are used based on their suitability for the final product. Some common materials are:
- Steel: Highly durable, suitable for high-volume production.
- Aluminum: Lightweight, cost-effective for smaller runs.
- Plastic: Used for low-cost, low-volume production and rapid prototyping.
Each material brings unique properties that influence the tool's performance and the final product quality. Therefore, selecting the right material is essential for creating effective moulds.
Quality Control Processes
Quality control is paramount when it comes to mould tooling. Reliable manufacturers implement multi-stage quality control processes, including:
- Incoming Material Inspection: All raw materials are tested for quality before use.
- In-Process Quality Checks: Continuous monitoring during production to identify defects early.
- Final Inspection: Comprehensive testing of the finished mould against design specifications.
- Documentation and Reporting: Proper documentation of inspection processes to maintain accountability.
These rigorous quality control processes ensure that the moulds produced are robust and reliable, ready for integration into the manufacturing process.
Advanced Technologies in Mould Tooling
To stay competitive, many mould tooling manufacturers in China adopt cutting-edge technologies such as:
- CNC Machining: Offers high precision and excellent repeatability for mould making.
- 3D Printing: Allows for quick prototyping and adjustments in design.
- Simulation Software: Helps in visualizing the mould performance and predicting issues before physical production.
The incorporation of these technologies not only enhances the efficiency of the manufacturing process but also improves the overall quality of the moulds produced.
Choosing the Right Mould Tooling Manufacturer
When looking for a mould tooling manufacturer, consider the following factors:
- Experience: Choose manufacturers with a proven track record in mould tooling.
- Client Reviews: Check testimonials and reviews from previous clients to gauge reliability.
- Technical Capabilities: Ensure they have the necessary equipment and technology to meet your requirements.
- Customer Service: Opt for a manufacturer that provides excellent communication and responsive support.
- Location: Consider logistical aspects and the benefits of working with a nearby manufacturer versus one far away.
Taking the time to research and evaluate potential manufacturers will pay off in the long run through improved product quality and reliability.
Conclusion
In conclusion, mould tooling is a vital component of modern manufacturing, and choosing the right mould tooling manufacturer in China can significantly impact your business's success. With a focus on quality, innovation, and cost-effectiveness, manufacturers in China are well-equipped to meet the demands of a global market.
At Deep Mould, we take pride in delivering outstanding mould tooling solutions that cater to diverse industries. Whether you are looking for customized solutions or standard designs, our team is here to help you achieve your manufacturing goals efficiently and effectively.
Ready to take your manufacturing capabilities to the next level? Contact us today at Deep Mould to learn more about our services and how we can assist you in your mould tooling needs.
© 2023 Deep Mould. All rights reserved.
mould tooling manufacturer china