Understanding the Role of an Injection Molding Maker in Metal Fabrication
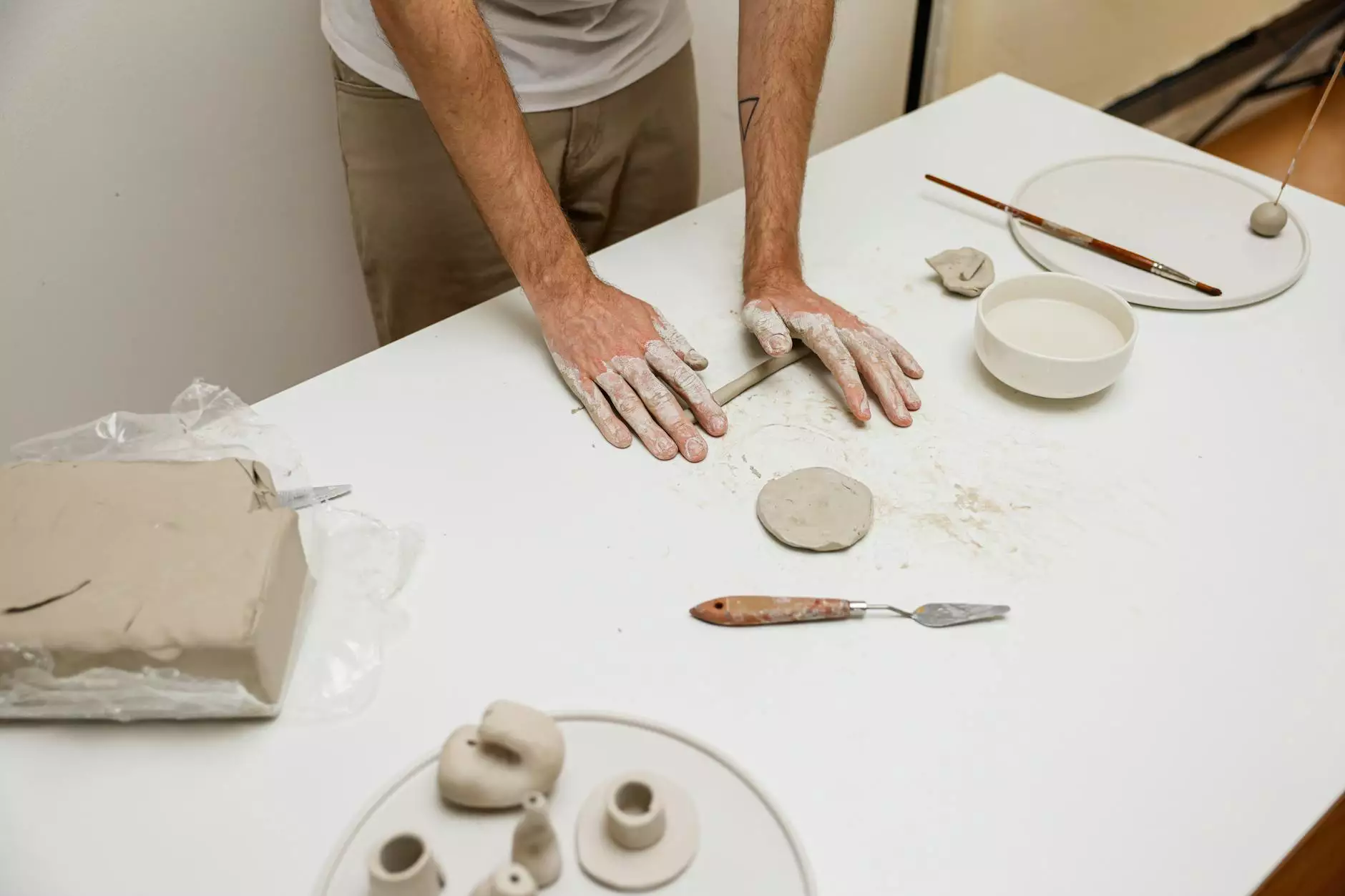
The injection molding maker plays an essential role in the manufacturing landscape, particularly in the realm of metal fabrication. The process of injection molding has evolved significantly over the years, becoming a linchpin in producing high-quality, complex parts efficiently. This article delves deep into the importance of injection molding, the processes involved, and how it fits into the larger picture of metal fabrication.
What is Injection Molding?
Injection molding is a manufacturing process used for producing parts by injecting molten material into a mold. This method is highly regarded for its efficiency and the high quality of the end products. While it is commonly associated with plastics, injection molding can also be applied to metals, particularly in processes known as metal injection molding (MIM).
How Injection Molding Works
The injection molding process includes several key steps:
- Material Selection: Choosing the right material is crucial; options can range from thermoplastics to metals.
- Mold Design: A precise mold is engineered to create the desired shape of the part.
- Injection: The molten material is injected into the mold under high pressure.
- Cooling: The injected material cools and solidifies in the mold.
- Demolding: The finished part is ejected from the mold.
The Advantages of Using an Injection Molding Maker
Utilizing the services of an injection molding maker provides several compelling advantages:
1. High Efficiency and Speed
Injection molding is one of the fastest manufacturing processes available, allowing for mass production of parts in a fraction of the time required by traditional methods. This efficiency can significantly reduce time-to-market, an essential factor for businesses in today's competitive landscape.
2. Precision and Consistency
The precision of injection molding matches the demands of high-quality metal fabrication. Each part produced can meet stringent specifications, ensuring consistency across batches. This capability is vital for industries like automotive and aerospace, where component reliability is paramount.
3. Cost-Effectiveness
While the initial investment in molds and machinery can be significant, the cost per unit decreases with larger production runs. Once the processes are established, an injection molding maker can manufacture parts at a lower cost compared to other manufacturing techniques.
4. Versatility in Design
Injection molding allows for complex geometries that other manufacturing methods struggle to achieve. This design flexibility enables engineers to innovate and create parts tailored to specific function and performance requirements.
5. Reduced Material Waste
Injection molding is a closed-loop process that generates very little waste material compared to traditional machining operations. This efficiency not only helps reduce costs but also plays a role in sustainable practices—an increasingly important consideration for manufacturers today.
Metal Injection Molding (MIM): A Specialized Application
While traditional injection molding is typically associated with plastic parts, Metal Injection Molding (MIM) has emerged as a significant advancement in the field. MIM combines the principles of injection molding with powdered metallurgy, allowing for the production of metal parts that are both complex and precise.
Process Overview of MIM
The MIM process includes several specific steps:
- Feedstock Preparation: A mixture of metal powder and binder is created.
- Injection Molding: The feedstock is injected into a mold, forming a near-net-shape part.
- Debindering: The binder is removed through thermal or chemical processes, leaving behind a porous metal part.
- Sintering: The part is heated in a controlled atmosphere to bond the metal particles, densifying the part to final dimensions.
Applications of Injection Molding in Metal Fabrication
An injection molding maker can cater to a variety of industries. Here are some notable applications:
1. Automotive Industry
In the automotive sector, injection molding is used for producing components like gears, connectors, and housing parts. MIM provides the ability to manufacture lightweight yet strong parts that offer significant performance advantages without the excessive weight.
2. Medical Devices
Injection molded metal parts are increasingly evident in medical devices, where precision is essential. Components such as surgical instruments and implants require complex geometries that injection molding is well-suited to produce.
3. Aerospace Applications
In aerospace, components need to withstand high stress and complex loads. Injection molding, particularly MIM, allows manufacturers to produce lightweight, high-strength parts that meet stringent safety and performance standards.
Choosing the Right Injection Molding Maker
Selecting an appropriate injection molding maker is a critical decision for any business engaged in metal fabrication. Consider the following factors:
1. Experience and Expertise
Assess the maker's experience in the field, especially with the specific materials and manufacturing techniques relevant to your needs. Expertise can greatly influence the quality of the final product.
2. Quality Assurance Procedures
Inquire about the quality control measures in place. A reputable maker will have rigorous testing protocols to ensure that all produced parts meet industry standards.
3. Technological Capabilities
Evaluate the technological competencies of the maker. Advanced machinery and software can streamline the design and production processes, enhancing the overall efficiency and quality of the output.
4. Capacity and Scalability
Consider the production capacity of the injection molding maker. Their ability to scale operations according to your demand is vital, particularly if you foresee growth or fluctuating needs.
5. Customer Support and Communication
A strong, communicative partnership can facilitate better problem-solving and quicker adjustments throughout the manufacturing process. Look for makers that prioritize customer service and engagement.
Conclusion
In conclusion, the role of an injection molding maker is foundational to the success of modern metal fabrication. With the speed, efficiency, precision, and versatility it offers, injection molding remains a vital methodology for producing complex components across various industries. As technology advances, so too will the applications, underscoring the importance of aligning with a proficient molding partner for your manufacturing needs. Embracing these innovative processes will not only enhance production capabilities but also contribute to significant competitive advantages in today’s marketplace.
For more information about injection molding and how it can benefit your business, contact us at deepmould.net.